Offshore Engineering
Our Design Services include development of concepts and solutions consisting of floaters to address precise offshore operational requirements.
Multi-Axis Stability
Series 5&6 are Bethlehem type mat supported existing Jack up Drilling Units which are converted to Offshore Production Units for operation in Offshore Malaysia. On conversion the vessels are classed with BV as Offshore Self-Elevating Unit – Production, Offshore Peninsular Malaysia with a design life of 10 years. The detailed Conversion Engineering of the project involved the following.
Naval Architecture
- Weight & COG Control
- Lightship Estimation
- Inclining Experiment
- Motion and Acceleration Analysis for Transit Route
- Accommodation Layout Engineering
- 3D Space Engineering
- Hazardous Zone and Safety Engineering
- Marine Operation Manual
Structural Engineering
- Dynamic Analysis of the Global Elevated Model
- Elevated Leg Strength Analysis
- Leg Reinforcement by flat bar strapping
- Jack House Analysis
- Initial Weibull Fatigue analysis of leg
- Spectral Fatigue analysis of leg and leg–mat connection
- Helideck Hull Interface Analysis
- Structural Outfitting Engineering
- 120′ Burner Boom, Kingpost & Heat Shield Analysis
The JUB is of size 64 M length and 41.4 Breadth used in offshore construction in Middle East Asia
Initially a FEED study was conducted to establish the feasibility of conversion and extent of modifications.
The owner required higher elevated loads, replacement of eight legs with 4 cylindrical legs, replacement of pneumatic gripper jacking system with rack and pinion system, Power Upgrade, addition of a CAP 437 compliant Helideck, post conversion design life of 15 years and MODU compliance.
Based on the FEED studies, the following were decided:
- Breadth Jumboisation by 8 m
- Circular cylindrical legs with opposed pinions
- Floating jacking system
- Repositioning of legs to the newly added sponsons
JUR A an existing Jackup Drilling Unit is being converted to an Offshore Production Installation. On completion of FEED studies and establishing the feasibility, detailed Engineering is being carried out.
Naval Architecture
- Weight/CG Determination of the lightship
- Extensive Stability Analysis – covering Intact & Damage stability carried out
- 3D Space engineering taking into account MODU Safety Requirements
- Space arrangements complying all loadline requirements, watertight integrity/subdivision requirements and hazardous area requirements
Structural Engineering
- Dynamic Analysis of the Global Elevated Model
- Linear Extreme Wave Time Domain Analysis to calculate the wave loading including dynamic response on the legs
- Elevated Leg Strength Analysis considering soil springs
- Leg Reinforcement iwo the leg guides
- Spud Can / Leg Soil Collapse Analysis
- Global elevated hull analysis
- Buckling and Ultimate Strength Analysis of Hull Panels
- Leg Well & Jack House Analysis for increased interface Loads
- Spectral Fatigue analysis of leg but welds, tubular connections, leg – spud can interface
- Fatigue Analysis of the Hull, Jack House and Leg Well
- Seismic Analysis of the Elevated Unit
- Crane Pedestal Design and Hot Spot Fatigue Analysis
- Raw Water Tower Design and Engineering
- Helideck Upgrade as per CAP 437
- Top Side Structural Outfitting
- Living Quarters Tier Addition and Block Engineering
Interface Engineering
- System design of all utilities to the Top side
- System design for the Emergency Power supply
- System Design for Safety comprising fire water and CO2 systems
Layout Engineering
- 3-D models & Clash Analysis
- Developed layouts for Switch gear rooms and Pump rooms
- Layouts designed for minimizing Hazardous zone requirements
- Layouts also designed for Proper material handling
- Development of material handling facilities
Marine/Process Engineering
- Developed all Utilities P&IDs
- Pump & Other Equipment sizing
- Flow calculations and pipe sizing
- Extensive studies carried out to establish/utilize the existing pumps and other systems
Electrical & Instrumentation Engineering
- Emergency Generator sizing
- Load lists
- Lighting Arrangements
- Transformer sizing
Safety Engineering
- Compliance with MODU Code safety
- Compliance with ABS rules on Offshore Installations
- Participation/Compliance in HAZOP/HAZID/SIL studies
A. JUR GSF a 300 ft drilling unit
This unit was in cold storage for two years in Malaysia and various Engineering scopes were carried out for reactivating the rig.
- Fast Rescue craft installation
- Helifuel Tank Storage
- Extension of Accommodation deck to install an Accommodation container
- 60T SWL Panama chock on port & stbd side
- Gymnasium
- Choke & Kill line platform
- Crew Baggage iwo Helideck
- Substructure repair plan & FE analysis
- Shaker Deck analysis
- Centrifuge Deck analysis
B. JUR GSF a 300 ft drilling unit
JUR CD a Marathon Letourneau 116C design jackup drilling unit built in year 1992 required a number of modifications for deployment in the field.
Works carried out
- Strength Calculation of Platform for the loads of OSUPA unit
- Calculation of SWL of Trolley Beams of BOP
- Trolley Beam in pump room
- Installation of Escape route from derrick
- Installation of a walkway to reach Monkey Board
Structural Outfitting Engineering is being carried out for a brand new Semisubmersible Drilling Tender, being designed by a Singapore-based leading Submersible designers in compliance with ABS MODU classification.
Structural design and engineering of foundations and supporting structures of various outfits are carried out based on the vendor documents and machinery arrangement drawings provided by the designer.
- Mooring Fairlead Foundation
- Anchor Racks and Foundation
- Crane Columns and Reinforcement
- Genset Foundations
- Mud Pump Foundation
- Cementing Unit Foundations
- PTB Foundations
- Life Boat Platform
- Mooring Winch Foundation
- Mooring Stowage Winch Foundations
- Helideck Truss and Support Structure
- Crane Boom Rests
- Fender Bumper Reinforcement
- Towing Bracket Foundations
- Bollard and Chock Foundations
Naval Architecture
- Finite Element Analysis of Foundations and Support Structure
- Panel Buckling and Ultimate Strength Analysis
- Shell Buckling and Ultimate Strength Analysis for Crane Column
- Hot Spot Fatigue Analysis of Foundations experiencing cyclic loading (Crane Columns, Mooring Winch Foundations and Fairlead Foundations)
- Dynamic and Resonance Analysis of Foundations with exciting Machineries (Genset, Mud Pump and Cementing Unit Foundations)
- Joint Strength Analysis of Tubular Joints
- ABS MODU Rule compliance
- Marine systems Specifications.
- Marine demand Calculations for various systems
- Marine Philosophy preparation.
- RFQ preparation for Marine equipments
- Mechanical data sheets
- HVAC specifications and Engineering.
- Material Handling study (Marine)
- Piping specifications.
- Piping – P&ID
- Piping – PFD.
- Piping – PFD.
- Stress Analysis for critical lines.
- Safety Engineering – Specifications/Plans/Bill of material.
- Hazardous Area definition and Plan.
- Structural Fire protection.
- Escape Route.
- Fire Control & Safety Plan (Marine)
- Electrical Load List ( Basic & Detailed).
- Overall Electrical Single Line Diagram (Marine)
- UPS sizing calculation (Marine)
- Electrical cable sizing calculation (Marine).
- Data sheets for electrical items.
- Instrument Data Sheet (Marine)
- Instrument Index & I/O List (Marine)
- Telecommunication PAGA Layout (Marine)
- Cause and Effect Matrix (Marine)
- Hull Outfitting Specification
- UWILD Plan
- Anchoring and Mooring Fittings.
- LQ specifications.
- LQ general arrangement and Layout.
- LQ structural design and MTO
- General arrangement development based on functional/Operations philosophy
- Hull Basic design development & Lines Plan
- Intact Stability and Damage stability
- Hydrodynamics –( Motion, Acceleration RAOs) ,Wave Loading
- Mooring Analysis
- Hull structure specifications.
- Hull scantling assessment as per class (ISE)
- Hull Global analysis and Fatigue Analysis
- TSA analysis for Transverse strength
- Hull interface with Appurtenances structure design
- Detailed Weight estimate for Hull and weight control.
- Steel renewal Plan.
- RLEC specifications and Plan
- Comprehensive Hydrodynamic Analysis for Hull.
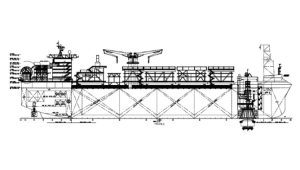
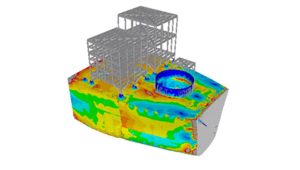
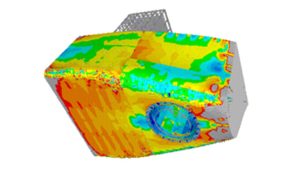
Using STOFAT module and DNV GENIE
OR
Using DLAFOS from ABS with FEMAP & NASTRAN
SESAM Suite
A comprehensive structural and hydrodynamic analysis software from DNV software. Comprising of Genie, Sestra, HydroD, WADAM, Stofat ,SIMO etc.
Eagle FPSO Suite
Used for the design and classing of ship-type Floating Production Installations (FPI), according to Rules for Building and Classing Floating Production Installations.
FEMAP & NASTRAN
3D FE Structural Modelling and Analysis software
GT Strudll
Structural analysis software, using finite element method.
GHS
A software system for the design and evaluation of all types of ships and floating structures.
SACS
SACS is a finite element structural analysis suite of programs for the offshore engineering industry.
PIPE NET
Tool to analyse the pipe flow characteristics like pressure drop, water hammer ,flow rate etc.
CEASAR II
Pipe stress analysis and support design tool
PDMS
3D modelling tool for intelligent modelling and visualisation for engineering & production
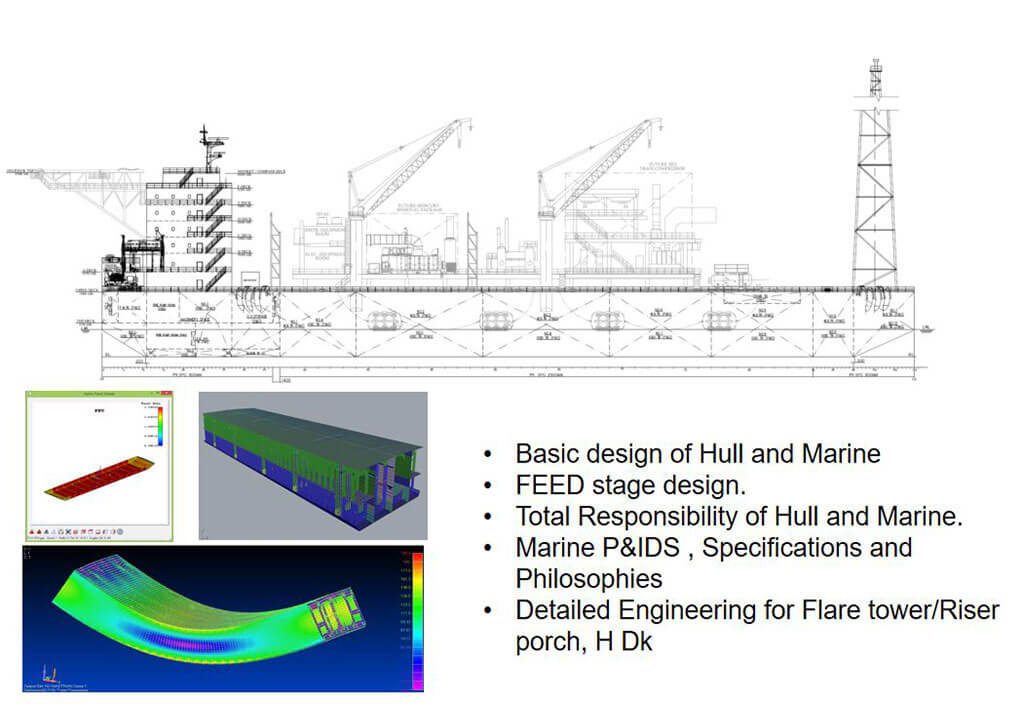